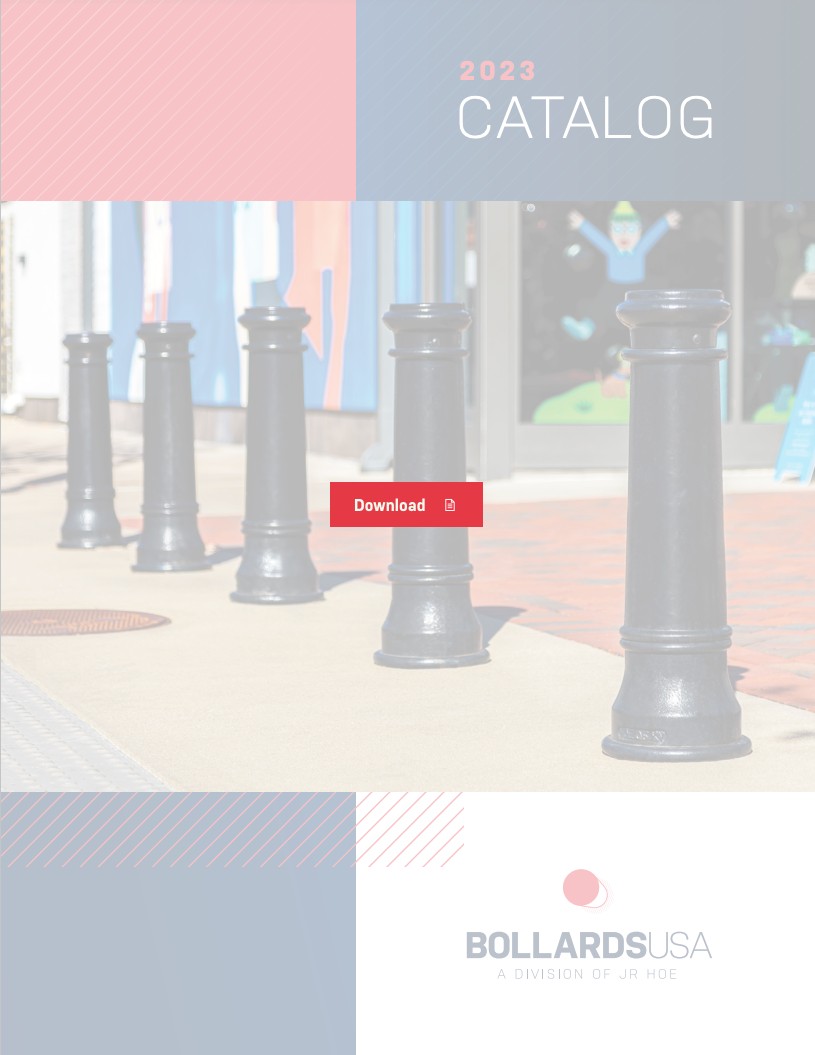
4” diameter, cast iron bollards. Predominately used in pedestrian areas.
View product line6” diameter, cast iron bollards. Function additionally as bicycle parking products.
View product line6” diameter, cast iron bollards. Available in safety & removable options.
View product lineCustom diameter, coated steel bollards. Alternate heights and top designs available.
View product line4”x4” square diameter bollards, available in cast iron and coated steel. Customizable cast top option available.
View product line3 ½” diameter bollards, available in cast iron & coated steel. Function additionally as bicycle parking products.
View product lineCustom diameter, stainless steel bollards. Alternate heights and top designs available.
View product lineK4/M30 crash-rated bollards. Cast iron & interior steel foundation system.
View product line